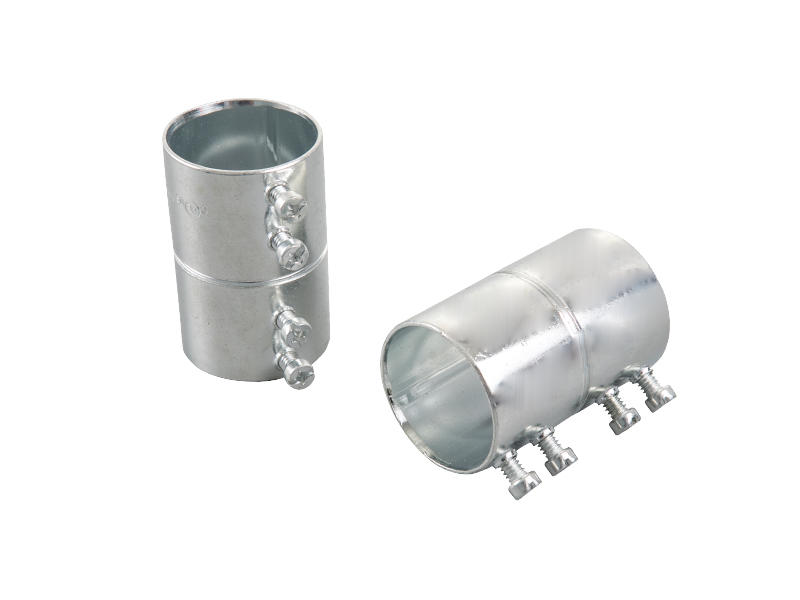
Zinc Die Casting Fittings have become the preferred components in the automotive, electronics, construction and other industries due to their high strength, precision formability and cost-effectiveness. However, corrosion problems may lead to component failure, safety hazards and even high repair costs.
1. Material optimization: Reduce corrosion risks from the source
The corrosion resistance of zinc alloys is closely related to their composition. Selecting high-purity zinc-based alloys (such as Zamak series) that meet international standards (such as ASTM B86) and strictly controlling the ratio of elements such as aluminum, copper and magnesium can significantly reduce microscopic galvanic corrosion. For high humidity or chemical exposure environments, modified alloys containing nickel or titanium are recommended to enhance the stability of the passivation film.
2. Surface treatment technology: Building multiple protective barriers
Passivation treatment: Through chromate or environmentally friendly chromium-free passivation agent (such as trivalent chromium process), a dense oxide film is generated on the surface of zinc die castings to block moisture and oxygen penetration.
Electroplating protection: For extreme environments, nickel (in accordance with ISO 2081 standard) or tin can be electroplated on the zinc substrate to meet both anti-corrosion and aesthetic needs.
Powder coating/epoxy coating: The polymer coating is covered with an electrostatic spraying process, which is suitable for outdoor equipment connectors, acid and alkali resistant and UV resistant.
Industry data: Zinc die-castings that have been double-treated with passivation + epoxy coating can extend their service life to more than 10 years in marine environments.
3. Design innovation: avoid structural weaknesses
The geometric design of zinc die-castings directly affects the corrosion rate. Engineers need to avoid sharp edges, blind holes or too thin cross-section thickness (recommended ≥1.5mm) to reduce electrolyte retention and stress concentration. The use of rounded corner transitions, homogeneous wall thickness design, and combined with mold flow analysis to optimize casting quality can eliminate local corrosion caused by micropore defects.
4. Environmental management and regular maintenance
Even with high-quality materials and processes, the use environment still needs to be controlled:
Avoid direct contact between zinc die-castings and dissimilar metals such as copper and steel to prevent electrochemical corrosion. If they must be combined, use insulating gaskets or sealants to isolate them.
In humid or polluted areas, it is recommended to deploy humidity sensors and regularly clean surface contaminants (such as salt and industrial dust).
Expert tips: Check the coating integrity of zinc die-castings every quarter, and use non-destructive testing techniques (such as eddy current testing) to identify potential corrosion points in advance.
5. Standardized testing: Verify anti-corrosion effectiveness
Before mass production, the feasibility of the solution needs to be verified through accelerated corrosion tests, such as:
Neutral salt spray test (ASTM B117): simulates the environment of marine or road de-icing agents.
Cyclic corrosion test (ISO 16701): combines multiple factors such as humidity, heat, dryness, and salt spray, which is closer to the real scene.
Cost-benefit analysis: The initial investment in anti-corrosion costs usually only accounts for 5%-8% of the total value of the component, but can reduce 80% of the subsequent replacement and downtime losses.
Corrosion protection of Zinc Die Casting Fittings is a systematic project that needs to run through the entire chain of material selection, process design, production control and terminal maintenance.